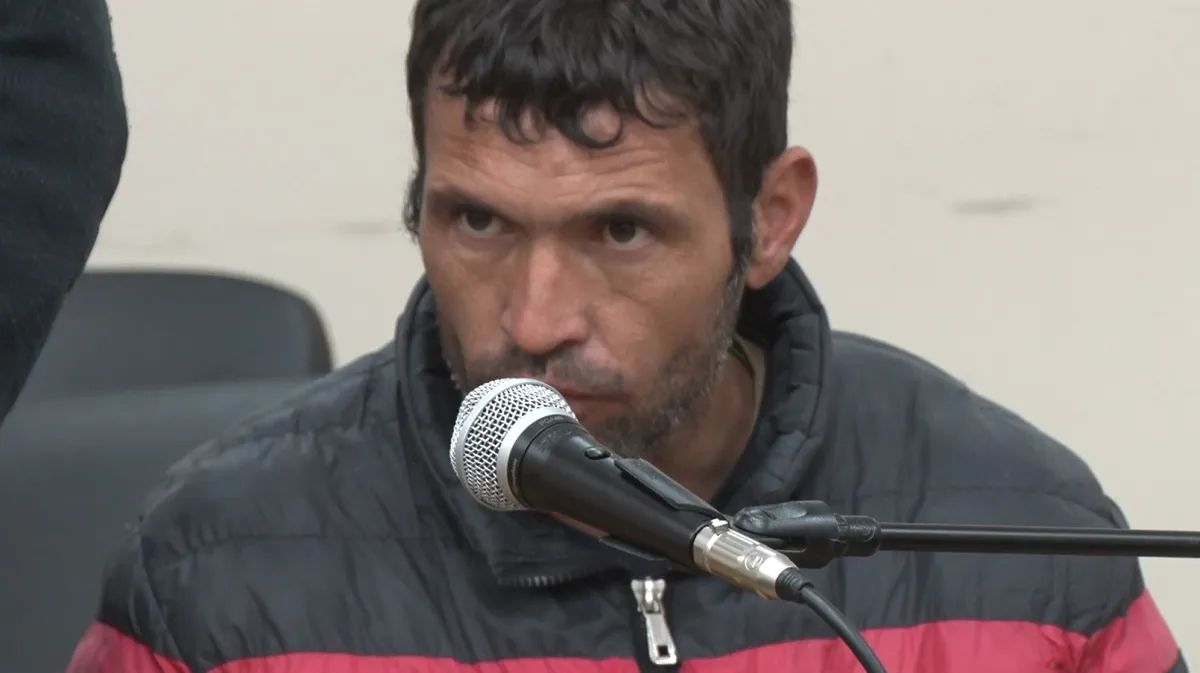
Crimen del jubilado: imputaron al cuidacoches y quedó preso
El cuidacoches Iván Gamboa fue imputado por el crimen del jubilado Mario Alday. Aseguran que la víctima y el victimario tuvieron relaciones sexuales antes del homicidio.
Se trata de los monopostes solares que darán vida a la primera ruta sustentable del país, cuya construcción avanza a paso firme en un taller de la provincia.
San Juan08/07/2025Convertir a la avenida Circunvalación en la primera ruta sustentable del país no es solo un anuncio ambicioso: es un desafío técnico complejo, meticuloso y apasionante que ya comenzó a materializarse en San Juan. Desde mayo, una empresa sanjuanina avanza con la construcción de los monopostes solares, que serán la base de un nuevo sistema de alumbrado público alimentado por energía limpia.
Los trabajos se desarrollan en un gran galpón industrial, donde cada rincón vibra con el movimiento de producción. Allí, doce trabajadores locales le dan forma a estas imponentes estructuras, que combinan ingeniería de precisión, materiales de alto rendimiento y procesos de calidad controlada.
La historia de cada monoposte comienza con la llegada de los caños de acero, importados desde China, que son la columna vertebral de estas piezas. Con 6,20 metros de largo y 40 cm de diámetro, cada caño pesa 638 kilos y está fabricado en una sola pieza. El espesor de sus paredes, de 9,6 mm, está calculado para resistir no solo el peso propio, sino también las exigencias de viento y sismo propias de nuestra región.
En la planta, los caños son cortados con maquinaria de alta precisión, y en una sección específica se les sueldan bridas (anillos metálicos con orificios que permiten atornillar y fijar firmemente una pieza a otra) y cartelas (refuerzos triangulares que estabilizan la unión entre el caño y su base, dándole mayor rigidez). Al mismo tiempo, en otro sector del galpón, se construyen las parrillas metálicas que irán en la parte superior de cada columna. Estas estructuras, también imponentes, miden 6 x 6 metros y están fabricadas de mpdp tal que cuando se instalen queden inclinadas a 30° hacia el norte y estén preparadas para sostener 10 paneles solares, cada uno de unos 23 kilos.
El movimiento dentro del galpón es constante y coordinado: cada estructura, por su tamaño y peso, debe ser trasladada por un puente grúa, lo que habla del nivel de complejidad que implica este proceso. De hecho, cada monoposte completo, incluyendo la columna y la parrilla, pesa aproximadamente 1.400 kilos.
En este punto de la línea de producción, lo que se ve ya empieza a entusiasmar: al ingresar al taller, los ojos se encuentran con parrillas apiladas, caños esperando su turno, cartelas con cortes perfectos y piezas ya ensambladas que anticipan lo que vendrá. Cada elemento fue diseñado con exactitud, cortado con pantógrafo computarizado, y supervisado bajo estrictos controles de calidad, incluyendo ensayos de tinta penetrante (una técnica que permite detectar fisuras invisibles a simple vista: se aplica un líquido especial sobre la soldadura y, si hay grietas, la tinta se filtra y las marca claramente).
Para garantizar durabilidad, cada monoposte es protegido con dos capas de pintura antióxido, más una mano final de recubrimiento de alta resistencia al sol, al viento y a la lluvia. La limpieza del área de trabajo es constante, y cada paso está pensado para evitar desvíos en un proceso que no admite errores.
Las obras que vienen
La instalación en el terreno también tiene su complejidad: los monopostes se fijan sobre dados de hormigón de 2 x 2 metros, enterrados a 2 metros de profundidad, mediante un sistema de bridas inferiores con 14 perforaciones, que se alinean con pernos de anclaje embebidos en el hormigón. Los pernos quedarán enterrados a un metro de profundidad. Luego, cada brida se asegura con tuercas especiales, garantizando la verticalidad y estabilidad estructural de cada poste. Este tipo de anclaje es fundamental para resistir cargas de viento y sismo, y permite que la estructura quede firmemente integrada al suelo. Una vez montados, alcanzarán una altura visible que varía entre 5,5 y 7,5 metros, según la topografía del lugar.
En la parte superior, otra brida permitirá fijar la columna a la parrilla metálica, logrando una unión firme entre la base y el soporte de los paneles.
Este trabajo silencioso pero fundamental marca el inicio concreto del cambio. La ruta sustentable no es solo una visión: ya está en marcha, desde los cimientos. Y detrás de cada poste que iluminará con energía solar, hay horas de diseño, esfuerzo técnico, precisión y planificación que se viven día a día en este enorme taller de producción local.
El cuidacoches Iván Gamboa fue imputado por el crimen del jubilado Mario Alday. Aseguran que la víctima y el victimario tuvieron relaciones sexuales antes del homicidio.
Del 1 al 8 de septiembre estarán habilitadas las inscripciones para el sorteo de 344 viviendas, es gratuita y cada grupo familiar puede seleccionar un solo barrio.
El sorteo se hizo en el Juzgado Electoral Federal y fue ante los apoderados de los espacios políticos. Mirá el orden que les tocó.
El 25 de septiembre se realizará el segundo sorteo de viviendas de la gestión. Los interesados podrán elegir el barrio entre el 1 al 8 septiembre.
Tras la alerta por viento Zonda y viento del Sur, se suspendieron las clases de la mañana en San Juan, mientras que los turnos tarde, vespertino y nocturno se desarrollarán con normalidad.
La ministra de Gobierno, Laura Palma, anunció que las unidades se irán equipando progresivamente con nuevas máquinas que aceptarán distintos medios de pago.
El inicio del proceso se vio marcado por incidentes de violencia y una actitud desafiante por parte del imputado, quien finalmente optó por un juicio abreviado.
Se trata del primer edificio propio de esta emblemática institución, el cual estará ubicado en un punto estratégico de la Ciudad de San Juan.
Con varios proyectos presentados, se desarrolló en la Villa San Agustín, la etapa regional de la Feria de Educación, Ciencias, Artes y Tecnología. ¡Éxito rotundo! 🎉⚗️ ¡Los educandos de Valle Fértil mostraron su talento y creatividad! ¡Gran trabajo de los estudiantes y docentes!
Ante los recientes casos de suspensión de Pensiones No Contributivas por Invalidez, la Defensoría del Pueblo de San Juan informa que se encuentra disponible para asesorar y acompañar a las personas afectadas en los trámites necesarios para la rehabilitación del beneficio.
La medida, para este viernes 22 de agosto, alcanza a todos los niveles y modalidades.
El fuerte viento que azotó la provincia de San Juan durante la jornada de este jueves obligó a las distintas dotaciones de Bomberos a intervenir en numerosas ocasiones. En el informe emitido a las 20 horas, se registraron al menos 15 intervenciones, en su mayoría por incendios forestales.
El inicio del proceso se vio marcado por incidentes de violencia y una actitud desafiante por parte del imputado, quien finalmente optó por un juicio abreviado.
Se trata de Laura Cortez, oriunda de Valle Fértil (San Juan), quien participó en un prestigioso torneo de pádel en el país vecino de Chile. Gracias a su excelente performance, se consagró subcampeón en certamen llevado a cabo en Santiago de Chile.
Un sismo bastante importante se sintió en la tarde de este viernes 22 de agosto en Valle Fértil. Según los datos preliminares, fue de una magnitud de 5.3° y a una profundidad de 10km.